Electroform 스텐실이 초미세 피치에 유리
니켈 도금 스텐실이 차세대 기술
플립칩 웨이퍼 범핑에 있어서 솔더 페이스트 스텐실 프린팅 방법은 다른 무엇보다도 비용 효율성과 SMT 어셈블리 라인 내에 이미 존재해 있는 프린팅 설비와의 호환성이라는 이점을 제공한다. 전통적인 스텐실 프린팅 기술을 활용한 최신 웨이퍼 범핑은 주변 정렬구조 경우 약 120㎛ 피치, 면정렬(area array)의 경우는 약 150㎛ 피치이다. 초미세 파인피치(<120㎛) 웨이퍼 범핑의 능력과 관련해서 여러 자료에서는 두드러진 기술적 향상이 보고되었다. 이러한 진일보는 칩이 3년마다 4배씩 증가한다는 Moore의 법칙에 비추어 볼 때 특히 매우 의미 있는 현상이다. 그러나 UFP 범핑 진일보는 매우 미세한 페이스트와 스텐실 제조기술이 동반되지 않으면 현실화될 수 없다. 초미세한 Type 7 페이스트(2~11㎛)와 최신의 Type 8(2~8㎛) 페이스트의 등장뿐만 아니라 매우 작은 개구 치수를 지닌 매우 얇은 electroform 스텐실 개발의 발전은 UFP 웨이퍼 범핑 영역에서 연구를 촉발시키는 중요한 계기가 되었다.
스텐실 프린팅은 전통적으로 값 비싼 증기 및 전기도금 프로세스(evaporation and electroplating processes)에 비해 경제적인 이점을 제공한다는 점 때문에 플립칩 범핑 공정용으로 선정될 가능성이 있다. 본고에서는 100㎛ 피치 그리고 특히, 60㎛ 피치의 UFP(Ultra-fine-pitch)로 주변 정렬 구조(peripheral array structures)의 6인치 웨이퍼 범핑의 모든 공정 단계에 있어서 진일보한 기술적인 과제를 다룬다. 혁신적인 electroform 스텐실은 20㎛ 이하의 두께로 제조되어 왔다. Sn63/Pb37 공정솔더의 Type 7(2~11㎛)와 Type 6(5~15㎛) 페이스트 모두 100㎛ 피치 웨이퍼 범핑에 성공적으로 적용되어 왔다. 25㎛ 스텐실 두께를 이용한 범핑 공정은 Type 7과 Type 6 페이스트에서 각각 42.3㎛±3.8㎛과 43.6㎛±3.5㎛의 범프 높이를 생성해 냈다. 새롭게 개발된 Type 8 페이스트(2~8㎛)은 60㎛ 피치의 주변 접착물이 있는 범프 칩들에 처음으로 사용되었다. 20㎛ 두께의 electroform 스텐실이 35㎛ × 80㎛의 장방형 개구 모양으로 사용되었다. 60㎛ 피치에서 프린팅은 매우 유망한 결과를 가져왔으며, 정확하고 견고하며 얇은 스텐실을 제작하기 위한 electroform 기술의 능력을 입증해 왔다. 60㎛ 피치에서 범프 높이는 28㎛±3㎛으로 측정되었다. 본고에서는 초미세 페이스트의 프린팅 거동, 자체 리플로우 및 슬럼프 특성과 같은 UFP 테크놀로지의 앞선 발전에서의 공정 이슈들뿐만 아니라 스텐실 제조 논의, UFP 범핑에 있어서 프린팅 머신 얼라인먼트 이슈까지 들어다 볼 것이다.
서문
플립칩 테크놀로지의 가장 큰 매력은 첨단 반도체 애플리케이션의 필수 요구사항인 강력한 전기 성능, 높은 열 전도성, 작은 사이즈 그리고 높은 I/O 수를 실현한다는 점이다. 그러나 플립칩 배선 기술을 향하는 중요한 변화는 생산비용 절감, 신뢰성 향상 및 비용 효율적인 고밀도 기판 기술 등의 성취가 근간이 되어야 한다. 저가의 플립칩 범핑 테크놀로지는 솔더 범프 형성을 목적으로 솔더 페이스트의 스텐실 프린팅과 함께한 UBM(under bump metallization)을 위한 무전해 니켈 도금 프로세스의 구현으로써 현실화되기 시작했다.
플립칩 웨이퍼 범핑에 있어서 솔더 페이스트 스텐실 프린팅 방법은 다른 무엇보다도 비용 효율성과 SMT 어셈블리 라인 내에 이미 존재해 있는 프린팅 설비와의 호환성이라는 이점을 제공한다. 전통적인 스텐실 프린팅 기술(레이저-절단 스틸 및 니켈-electroform 스텐실)을 활용한 최신 웨이퍼 범핑은 주변 정렬구조 경우 약 120㎛ 피치, 면정렬(area array)의 경우는 약 150㎛ 피치이다. UFP(Ultra Fine Pitch, <120㎛) 웨이퍼 범핑의 능력과 관련해서 여러 자료에서는 두드러진 기술적 향상이 보고되었다. 이러한 진일보는 칩이 3년마다 4배씩 증가한다는 Moore의 법칙에 비추어 볼 때 특히 매우 의미 있는 현상이다. 그러나 UFP 범핑 진일보는 매우 미세한 페이스트와 스텐실 제조기술이 동반되지 않으면 현실화될 수 없다. 초미세한 Type 7 페이스트(2~11㎛)와 최신의 Type 8(2~8㎛) 페이스트의 등장뿐만 아니라 매우 작은 개구 치수를 지닌 매우 얇은 electroform 스텐실 개발의 발전은 UFP 웨이퍼 범핑 영역에서 연구를 촉발시키는 중요한 계기가 되었다.
본고에서는 최신의 발전사항과 electroform 스텐실 테크놀로지에서 등장하는 이슈들을 심도 있게 논의한다. 100㎛과 60㎛ 피치로 6인치 웨이퍼의 범핑을 위해 사용한 Type 6와 Type 8 솔더페이스트 각각의 UFP 스텐실 프린팅에 대한 연구 결과를 소개한다.
기술 구현
웨이퍼 디자인 & 화학 금속화
본고에서는 6인치 직경의 웨이퍼를 사용했다. 100㎛ 피치의 웨이퍼는 680㎛의 두께를 가지고 있는 반면, 60㎛ 피치의 웨이퍼는 320㎛의 두께를 보였다. 100㎛ 피치 웨이퍼는 5㎜ × 5㎜ 사이즈의 540개 칩으로 구성되어 있다. 각 칩은 주변 배열로 정렬된 패드에 176개의 I/O를 가지고 있다. 총 95,040개의 패드가 웨이퍼 상에 존재한다. 패드는 직경 40㎛의 정방형 모양을 보였다. TUB의 무전해도금 Ni/Au 도금 기술이 Al 금속 패드 상의 2㎛ Ni/80㎚ 플래시 Au(칩 패시베이션 레이어 전체)의 높은 UBM 패드 침전을 위해 사용되었다. 칩 패시베이션 레이어 상의 Ni/Au UBM 패드의 측면 겹침은 또한 양면에서 2㎛이다. 무전해 화학 금속화 프로세스는 최종적으로 44㎛ UBM 패드 사이즈를 생성한다. TUB의 무전해 Ni/Au 테크놀로지 방법(ENIG)의 자세한 설명은 여러 자료에서 찾아볼 수 있다. 이에 상응하여, 60㎛ 피치에서 주변 정렬 구조의 웨이퍼는 칩당 296개의 패드를 가진 5㎜ × 5㎜ 사이즈의 557개 칩을 가지고 있다. 총 170,792개의 패드가 존재한다. Al 패드 상 패시베이션 개구는 20㎛이고 동일한 ENIG 프로세스가 칩 패시베이션 레이어 전체에 4㎛ Ni/80㎚ Au 침전을 위해 적용하였다. Ni/Au 적용이후 웨이퍼의 UBM 사이즈는 28㎛이다. 그림 1은 60㎛ 피치에서 Ni/Au UBM을 보여주고 있는데, ENIG 프로세스가 매우 작은 웨이퍼 피치에서 적용 가능함을 입증하고 있다.
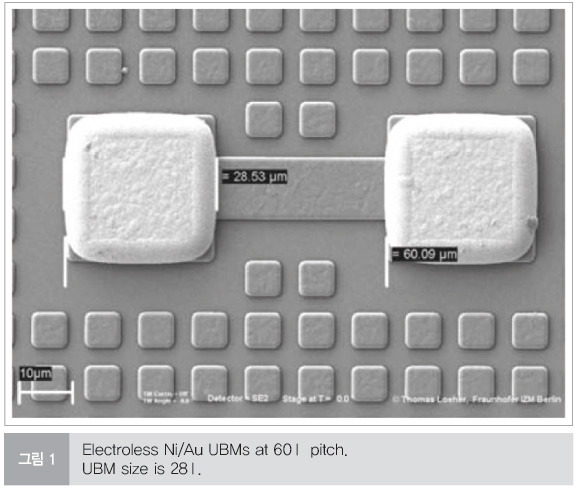
스텐실 디자인 규칙 & 스텐실 제조방법 선정
스텐실 제조 테크놀로지의 선정 기준 요인으로는 개구벽 품질, 치수 일관성, 위치 정확도 그리고 스텐실 생산비용을 꼽을 수 있다. 80㎛ 및 60㎛ 피치에서 UFP 구조의 스텐실 프린팅에 관한 이전의 연구에서는 레이저-컷 steel 스텐실의 매우 큰 잠재성을 보여주었다. 하지만 레이저 스텐실 제조업체의 기술적인 숙련도와 미세조정 가능한 레이저 건의 이용에 따라 개구 품질이 좌우된다는 점은 여전히 남아 있다. 레이저-컷 프로세스는 더욱 더 작아진 스팟 사이즈와 water guided 레이저 절단 기술을 포함한 스텐실 개구의 품질을 더욱 향상시키기 위해 발전을 거듭해 왔다. Electroform 기술과 비교해, 레이저-컷 스텐실의 한 가지 장점은 절단 이전 프레임하는 공정에서 미리 인장되어서 스텐실 변형이 줄어든다는 점이다. 레이저-컷 프로세스는 순차적으로 진행된다; 따라서 설계에서 I/O 수가 증가하면 스텐실 제조시간 역시 늘어난다. 이는 많은 개구의 수를 지닌 미세 및 초미세(<120㎛) 피치의 웨이퍼 범핑 스텐실에서 중요한 단점이 될 수 있다. 홀의 수가 많아지면, 제조시간이 거의 비경제적인 수준으로 상승하기 때문이다. 게다가 절단 프로세스 동안의 열 용융에 의한 상호작용은 거친 내부 측면을 생성할 수 있으며, 이는 결국 더 큰 표면적 개구를 생성하며, 따라서 페이스트 방출을 최소화하는 경향을 보일 수도 있다.
또한, 절단 프로세스에서 발생된 열은 제조 과정 중 스텐실 휘어짐 현상이 나타나지 않도록 하거나 혹은 UFP 프린팅에서 요구되는 미세 웹을 손상하지 않도록 조절되어야만 한다. 전기연마된 스텐실은 전기화학적이거나 혹은 기계적인 폴리싱 방법을 활용하여 평탄화된 일반적인 레이저-컷 스텐실이다. 하지만 모든 금속 스텐실 타입들은 제조 이후 이 방식으로 처리될 수 있다.
대략 100개 레이저-절단 개구 당 3$의 비용과 UFP 구조에 필요한 많은 수의 개구를 고려할 때 비용 요인은 매우 중요하다. 대조적으로, 우수한 개구 벽면 품질과 웨이퍼 설계 당 합리적인 제조비용을 지닌 electroform 스텐실은 특히, UFP 웨이퍼 구조에 합리적인 대체 솔루션으로 여겨진다. 따라서 이번 연구에서는 스텐실 제작을 위해 electroform 테크놀로지를 선정하였다. UFP 연구는 초미세 피치의 레이저-절단 스틸 스텐실로 수행하였는데, 이는 연속적인 프린팅을 위해 우수한 견고성을 지니고, 우수한 개구 평탄도(smoothness) 및 치수 정확성의 electroform 제품의 성능을 입증하기 위한 것이다. 100㎛ 피치의 웨이퍼 경우, 50㎛ × 125㎛의 타원형 개구를 설계하였고, 25㎛의 호일 두께를 선택했다. 웨이퍼 범핑용 개구 디자인은 패드 상 효율적인 페이스트 이송을 위해 aspect(> 1.5) 및 area(> 0.66) 비율의 기존 규칙을 항상 고려하였지만, 페이스트 브릿지를 회피하기 위해 최소 이격 거리를 유지하는 것도 염두에 두었다.
UFP 범핑의 경우, 앞서 언급한 디자인 원리를 충족시키는 핵심 솔루션을 찾기가 매우 어렵다. 100㎛ 피치 웨이퍼용 디자인은 1.5의 aspect ratio와 0.71의 area ratio로 각각 산출하였다. 60㎛ 피치에서의 웨이퍼용 개구 디자인은 35㎛ × 80㎛의 타원형 개구 및 20㎛의 포일 두께를 채택했다. Aspect 및 area ratio은 각각 1.75와 0.61이었다.
UFP에서 electroform 스텐실 제조의 기술적 어려움 및 달성
통상적인 electroform 스텐실 제조 프로세스에서는 스테인리스 스틸과 같은 전도성 맨드릴(conductive mandrel)을 형성하는 것과 포토레지스트의 드라이 필름 레이어를 도포하는 것을 포함하고 있다. 이 포토레지스트 레이어는 포토패터닝되고 현상된다. 포토리소그래피 후에 맨드릴 상에 남겨진 포토레지스트는 개구 윤곽을 드러낸다. 그 다음 기판을 전기 도금 용액에 넣고 맨드릴에 전류를 가한다. 스텐실 생성을 위해 일반적으로 증착되는 금속은 니켈 또는 니켈 합금이다. 전기도금은 솔더 페이스트 스텐실을 제조하기 위해 앞서 언급된 다른 감산 기술과 달리 가산 공정이기 때문에 증착된 금속은 포토레지스트 몰드와 정확히 일치한다. 도금 후, 개구에 남아있는 포토레지스트를 제거하고 완성된 스텐실을 프레임화 할 수 있다.
기존의 electroform 스텐실은 몇 가지 단점이 있다. 첫째, 포토리소그래피 단계는 기판, 레지스트 재료 그리고 마스크 기술을 사용하는데, 매끄러운 벽면의 고선명 포토리소그래피를 구현하기 어렵다. 또한, 고전류 DC electroforming와 연동된다는 점은 두께 균일성 및 스텐실과의 불균등한 개스킷 형성이 프린팅 동안 빈약한 균일성을 초래할 수 있음을 의미한다. 마지막으로, 피치가 줄어듦에 따라 효율적인 페이스트 이송이 가능한 스텐실 두께가 되어야만 하는데, 매우 얇은 스텐실은 탄성 변형이 생길 수 있다. 웨이퍼와 스텐실 간의 우수한 정렬을 보장하는 중요한 요인이지만, 대부분의 스텐실 제공업체들은 제조 프로세스 중에 이러한 변형을 보정하지 않는다. 스텐실은 프린팅 프로세스에서 중요한 요소로 간주된다. 올바른 스텐실이 없으면 높은 수율의 제조 공정을 달성하는 것이 불가능하다. 스텐실은 해당 애플리케이션에 맞는 정확한 두께 균일성 및 개구 공차를 가지고 있어야만 한다.
MicroStencil社의 제품
MicroStencil Ltd.는 플립칩 및 웨이퍼 레벨 패키징 업계에서 주로 사용되는 대면적 정밀 electroform 스텐실 제작을 위해 새로운 MEMS 기반 제조 공정을 개발했다. 다른 기판 재료, 고해상도 마스크 및 포토레지스트 화학 물질을 사용하여 매우 높은 해상도의 개구 몰드를 생성하였다. 이것은 첨단 전기도금과 함께, 스텐실을 통해 균일하고 일관된 인쇄가 가능하도록 전체 활성 영역에서 높은 개구 공차, 부드러운 벽면 그리고 양호한 두께 공자를 가진 스텐실 생산할 수 있게 되었다.
초미세 피치 스텐실 생산에 있어서 직면한 두 가지 주요 문제점은 결함 없는 포토레지스트 몰드를 생성하고, 스텐실 상의 프레이밍 힘으로부터 변형을 보정하는 능력이다. 고해상도 포토레지스트 몰드를 생산하는 능력과 관련해, 모든 스텐실은 electroform을 포함한 모든 공정 단계에서 클래스 100 수준의 클린룸에서 제조했다. 또한, 고화질 포토레지스트와 포토마스크는 고해상도 포토리소그래피 프로세스를 통해서 확보했다. 그림 2의 a와 그림 2의 b는 60㎛ 피치의 electroform된 35㎛ × 80㎛ 개구의 매끄러운 면을 보여주는 SEM 현미경 사진이다. 그림 2의 a 및 그림 2의 b는 프린팅(‘웨이퍼 측면’) 동안 웨이퍼와 접촉할 스텐실의 매끄러운 면을 나타내고 있다. Cyberoptics Vantage 레이저 프로파일미터로 측정한 거칠기 측정치는 60㎛ 피치 및 100㎛ 피치 스텐실에 대해 각각 0.11㎛ 및 1.1㎛의 부드러운 측면 거칠기를 나타냈다. 그에 상응하여, 페이스트가 닫게 될 스텐실의 거친면(인쇄면)은 니켈 입자 구조에 따라 60㎛ 및 100㎛ 피치 스텐실에 대해 각각 0.73㎛ 및 0.83㎛의 거칠음을 가지고 있는 것으로 밝혀졌다. 100㎛ 피치에서 30㎛ 두께의 레이저-절단 스틸 스텐실은 electroform 스텐실보다 ‘인쇄면’이 0.51㎛ 약간 더 부드러웠다. 60㎛과 100㎛ 피치의 electroform 스텐실의 단면도는 각각 그림 3과 그림 4에서 보여주고 있다.
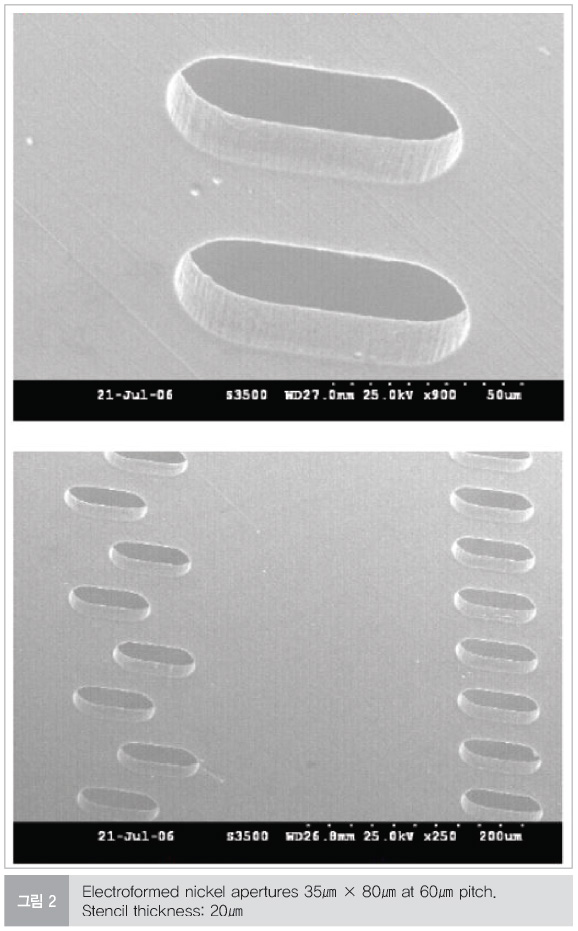
그림 3과 그림 4에서 상부 거친 면은 웨이퍼 프린팅을 위한 ‘인쇄면’이다. 개구 치수는 OKM Planaris 시스템으로 측정하였고, 종단면 분석에서 얻은 값과 그것을 비교하였다. 60㎛와 100㎛ 피치 스텐실 양쪽의 개구는 오리지널 Gerber 데이터와 단지 ±2㎛의 편차를 갖는 것으로 나타났다. 그림 3과 그림 4는 또한 틸트 없이 직선형 개구 벽을 생성할 수 있는 electroform 기술의 능력을 나타내고 있다. 이는 특히 프린트 침전 간의 이격 거리가 브릿지 방지를 위해 원래 설계대로 유지되어야 하는 UFP에서 특히 중요하다. 그림 4의 100㎛ 피치 스텐실의 경우에서는 약 4.4㎛인 양쪽 면의 작은 언더컷도 보여주고 있다. 이 언더컷은 그림 3의 60㎛ 피치 스텐실에서는 나타나지 않았다.
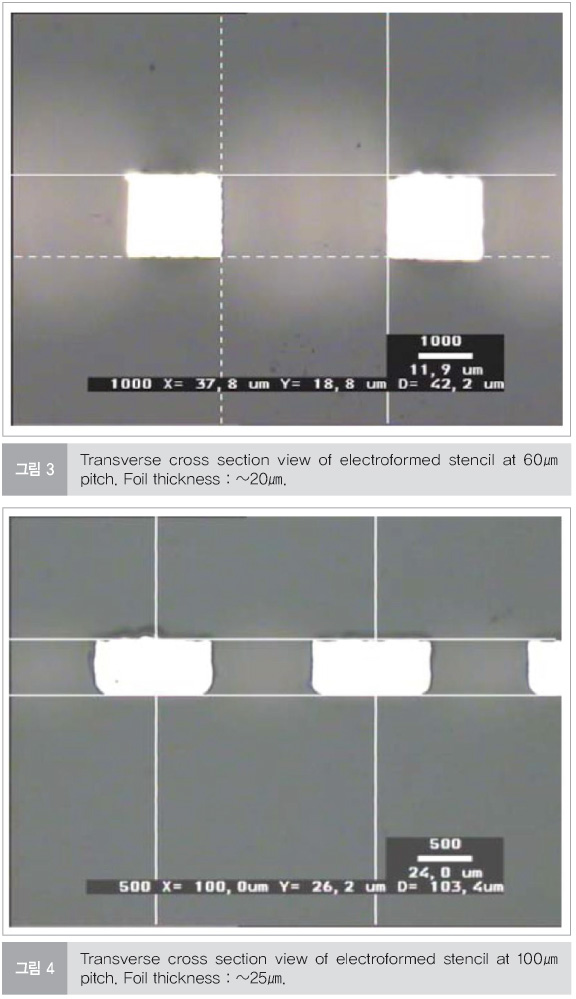
언더컷의 존재는 스텐실과 웨이퍼 사이의 양호한 씰링에 악영향을 미쳐서 스텐실 하부에 약간의 페이스트 크롤링(paste crawling)을 야기할 수 있다. 그럼에도 불구하고, 100㎛ 피치 스텐실에서 그다지 위태롭게 여지지 않는 것처럼 보이고, 이보다 더 중요한 점은 100㎛ 피치 웨이퍼 프린팅에서 보다 페이스트 스미어링(paste smearing)이 훨씬 더 중요한 60㎛ 피치 스텐실에는 존재하지 않는다는 것이다.
스텐실 변형 제어
영국의 그리니치 대학교과 헤리어트 와트 대학교(University of Greenwich and Heriot Watt University)의 이전 연구에 따르면 100㎛ 보다 얇은 스텐실은 프레임 공정 동안에 탄성 변형이 올 수 있다고 말하고 있다.
변형은 탄성이 있기 때문에 스케일링 보정 계수를 추가하여 제조 공정에서 보정할 수 있다. 일반적으로 얇은 스텐실은 알루미늄 프레임에 인장된 스크린 메쉬 상에 메쉬 형태로 올려졌다. 프레이밍 처리는 프린팅 프로세스를 위해 스텐실이 평평하게 당겨지도록 보장한다.
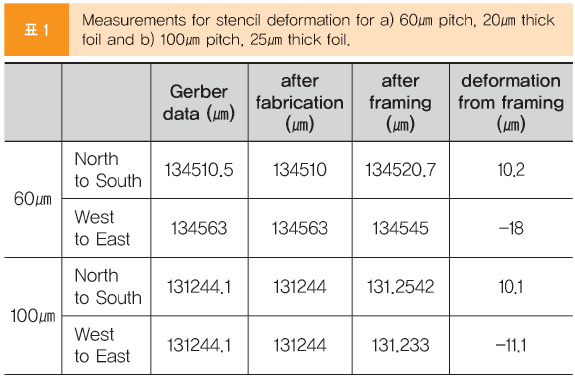
얇은 스텐실 변형에 대한 모델링 연구를 수행하였다. 모델링 데이터를 분석한 후, MicroStencil은 변형률을 측정하기 위해 서로 다른 개구 밀도를 지닌 25㎛, 50㎛ 및 75㎛ 두께의 electroform된 호일에 대한 조사를 실시하였다. 시뮬레이션에서는 어닐링된 니켈의 기계적인 특성을 적용해왔기 때문에 모델링 결과를 확인하는 것이 중요하다고 여겼다. 하지만 전기도금된 니켈이 도금 설정에 따라 잠재적으로 다른 특성을 보일 수 있다. 제조 시 변형을 보정하기 위해 이 재료 특성을 이해하는 것이 중요하다. 이 시험의 결과에 따르면, 스텐실은 x축과 y축에서 다르게 변형되었다. 따라서 각 축에서 개별적으로 보정해야만 한다. 이 차이의 원인은 electroforming 도중 니켈 결정의 이방성(異方性) 형성이다. 이 실험 세트의 데이터를 사용해, 이번 조사를 위해 60㎛ 및 100㎛ 피치 스텐실의 제조 프로세스에 보정 계수를 통합시켰다. 스텐실은 후속 변형을 측정하기 위해 설계 영역에 걸쳐서 프레이밍 이전과 프레이밍 이후의 스텐실을 측정하였다. 그 결과를 표 1에 기록하였다.
UFP electroform 스텐실 제작의 개선
본고에서 얇은 스텐실을 제조하는 것이 UFP 프린팅용 electroform 스텐실에 유망한 미래라는 점에 초점을 맞췄다. 게다가 포토리소그래피 파라미터의 최적화는 개구 측벽의 프로파일을 향상시킬 것이다. 스텐실 생산에 이 프로세스를 활용하면, 탁월한 결과를 얻을 수 있다고 입증되었으나 프로세스의 개선은 향후 스텐실의 품질 향상에 기여할 것이다.
이번 연구에 사용된 스텐실은 약 220HV 경도의 매우 부드러운 니켈 물질을 생성하는 표준 니켈 도금 조성물을 사용하여 도금되었다. MicroStencil은 최근 경도가 480HV 이상인 더 단단한 니켈을 생산하기 위해 도금 공정을 개선하였다. 이 단단한 니켈 재료는 프린팅 세기(printing forces)에서 마모되기 쉽지 않고, 프레이밍 및 프린팅 프로세스 양쪽에서 덜 변형된다.
다른 하나는 스텐실 표면 거칠기를 변경하기 위해 도금 설정을 변경하였다. 처음에는 거친 스텐실 상단 표면이 페이스트 롤링에 도움이 되지만, 매우 미세한 파티클의 솔더 페이스트로 개구를 충진하면, 솔더 스피어는 사실상 거대한 니켈 grain에 갇히게 되어 스텐실 표면 전체에 걸쳐 번짐 현상이 발생할 수도 있다고 생각했었다. 더 높은 프린트 압력을 사용함으로써 약간 보정될 수 있지만, 이 높아진 힘은 스텐실 변형을 가속화할 수 있다. 따라서 MicroStencil에서는 매우 부드러운 표면을 가진 스텐실을 생산하도록 도금 설정을 수정하였다.
솔더 페이스트 재료
이전의 보고서에서는, 솔더페이스트 Type 6(5~15μm)와 더 미세한 페이스트가 UFP 범핑(피치 <120㎛)에 적합하다고 말하고 있다. Type 6은 개구 설계에 기반을 둔 100㎛ 피치 웨이퍼 범핑까지 미미하게 사용될 수 있다고 이야기하고 있다.
이전의 연구 결과에 따르면, 우수한 페이스트 전달 효율을 위해 개구에 최소 5~7개의 입자가 수용되어야 한다. 실험 연구는 Type 7(2~11㎛) 페이스트의 100㎛ 피치에서 표준 Type 6(5~15㎛) 페이스트로 범핑한 결과를 비교하였다. 인쇄 및 범프 높이 분포의 차이는 중요하지 않았으므로 Type 7과 Type 6의 차별화는 필요하지 않았다. 웨이퍼 범핑용으로 이미 시장에 자리를 잡은 Type 6 페이스트는 300㎛에서 100㎛ 피치 범위의 웨이퍼 범핑 애플리케이션에 사용될 수 있다. UFP 애플리케이션(<120㎛)과 각 특수 애플리케이션에 따라 결정된 개구 설계를 기반으로 둔 경우, 새로운 Type 8 파우더가 제작되었고, 페이스트로써 제공되었다.
Type 8은 근본적으로 Type 6 파우더 크기의 절반인 2~8㎛의 파우더 사이즈를 가지고 있다. 본 연구에서는 60㎛ 피치(35㎛ × 80㎛ 개구)에서의 범핑을 위해 Type 8을, 100㎛ 피치(50㎛ × 125㎛ 개구)에서의 범핑을 위해 Type 6를 사용하였다. 표준 Type 6 페이스트는 상업적으로 이용 가능하지만, Type 8 페이스트는 개발 제품이다. 그러나 표준 Type 6 페이스트와 마찬가지로 새로운 Type 8에 동일한 화학적 성질을 사용하는 것이 제조자에 의해 결정되었기 때문에, 두 페이스트 양쪽의 유동학적 특성을 유사하게 설계했다.
10/sec의 전단 속도에서 양쪽 페이스트의 점도는 240±50 Pa sec이다. 그림 5에서는 플럭스 증발을 위한 짧은 가열 후 웨이퍼 상 60㎛ 피치의 프린트 침전물을 보여주고 있다. Type 8 페이스트의 파우더 사이즈는 2~8㎛인 것으로 확인되었다.
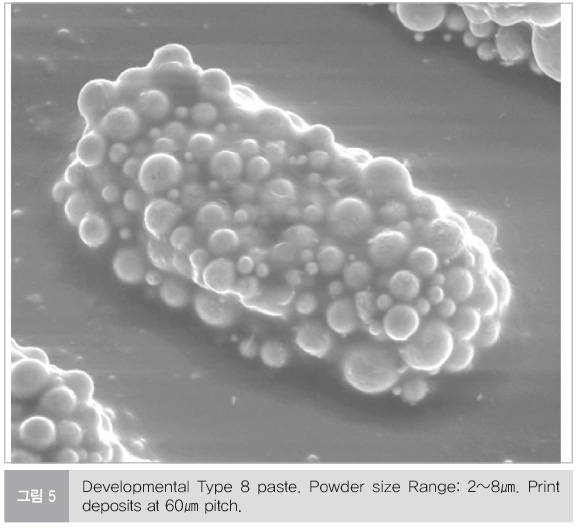
프린팅 결과 및 논의
Type 8 Sn63Pb37 페이스트(2~8μm)가 60㎛ 피치에서 6" 웨이퍼 프린팅에 사용되었고, MicroStencil Ltd.에서 electroform 스텐실을 제공하였다. Accuracy ±25㎛의 DEK 265 Horizon 스크린프린터로 프린팅하였다.
60° 각도의 고무 폴리우레탄 재질의 스퀴지가 프린터에 장착되었다. 폴리우레탄 스퀴지는 스테인리스-스틸 재질보다 electroform 스텐실에서 더 잘 작동한다.
앞서 언급했듯이, 니켈 electroform 스텐실의 본질적인 조도(粗度) 및 무광택 프린트 표면으로 인해 매우 높은 스퀴지 압력을 사용하지 않는 한 매우 깨끗한 프린트 스와이프(print swipe)를 얻는 것이 어렵다. 이러한 고압은 일반적으로 스텐실의 바닥면에서 플럭스 블리딩(flux bleeding) 및 페이스트 번짐을 생성하기 때문에 바람직하지 않다. 고무 스퀴지는 프린팅 시에 구부러지고, 니켈 표면으로부터 페이스트를 훨씬 잘 뜰 수 있다. 이 외에도 스테인리스-스틸 스퀴지는 매우 단단하고, 매우 얇은 스텐실 포일을 대번에 파괴할 수 있다. 그럼에도 불구하고, 더 견고한 니켈을 지닌 스텐실을 생산하고자 할 때, 스테인리스-스틸 스퀴지를 사용하는 경향도 있다. 금속 스퀴지는 폴리우레탄 스퀴지 이상으로 범프 높이 균일성을 향상시킬 수 있다.
250mm 길이의 폴리우레탄 스퀴지에 5~15mm/sec의 인쇄 속도와 3~4kg의 인쇄 압력을 적용하였다. 이러한 파라미터는 적용된 최소 압력과 적절한 개구 충진으로 깨끗한 프린트 스윕(print sweep)을 보장할 수 있다.
접촉 방식의 프린팅을 이용하였고, 120㎛보다 더 작은 피치의 웨이퍼 프린팅에 있어서 스냅-오프(snap-off) 프린팅에 비해 일반적으로 가장 적합한 선택이라고 할 수 있다. 실제로 60㎛ 피치에서 20㎛ 얇은 호일은 스냅-오프 프린팅 시 심각하게 휘어질 수 있고, 앞서 언급한 바대로 상당한 스텐실 변형을 초래한다. 대조적으로, 접촉 프린팅은 반복된 탄성 변형으로부터 얇은 호일을 보호할 수 있다.
60μm 피치의 프린팅은 웨이퍼 패드와 스텐실 개구 사이를 정렬시키는 것이 매우 어렵다. 3개의 피디셜 마크가 정렬을 위해 매번 사용되어 왔음에도 불구하고, TUB에서 기존 설비의 등록을 개선하기 위해 항상 오프셋이 사용되어야만 한다. 앞선 언급한 스텐실 변형은 매우 중요하다. 스텐실 프레이밍 이후 우선적으로 모니터링해야만 한다. 약간의 변형이 나타나면, 웨이퍼와 스텐실 간의 피할 수 없는 불일치를 초래할 수 있다. 프레이밍 프로세스로 인한 변형 외에도, 반복적인 프린팅 작업은 스텐실 신축의 원인이 될 수도 있다. 본 연구에서는 웨이퍼에 대한 프레임 스텐실의 정렬이 허용될 수 있도록 보장하기 위해 변형을 관찰하여 측정하였다. 20번 프린팅하고, 변형이 발생할 수 있는 스텐실을 수동으로 클리닝 이후, 항상 좋은 정렬을 이룰 수 있었다. 그림 6은 Type 8 페이스트를 적용하여 60㎛ 피치로 수행한 프린트 침전을 보여주고 있다. 침전 두께는 호일 두께와 동일하게 20㎛이었다. 침전은 상단면에서는 약 35㎛ × 77㎛, 하단면에서는 약 41㎛ × 84㎛의 치수를 보였다.
그림 3에서와 같이 개구 벽이 직선형이라는 사실에 기반을 두었을 때, 하단의 더 커다란 침전 치수는 해당 프린팅 조건 하에서의 페이스트 양 급감 아니면 웨이퍼 측면에서의 소량의 언더컷으로 인해 나타날 수도 있다. 상부 치수는 electroform 개구를 통해 Type 8 페이스트의 양호한 페이스트 방출을 나타낸다. 일부 페이스트는 직사각형 개구의 둘레에 있는 스텐실에 남아 있다. 침전물의 이격 거리는 15㎛~19㎛이다. 25㎛의 목표 이격 거리는 페이스트 슬럼프 특성으로 인해 달성되지 않았다.
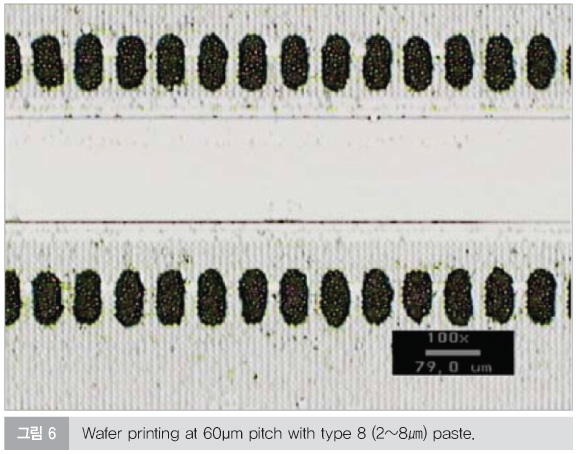
Electroform 스텐실에서의 Type 8 페이스트 방출은 매우 양호하다. Electroform 스텐실로부터 Type 8의 페이스트 방출에 있어서 최소한의 요구사항으로 알려진 개구 aspect (1.75)과 면적 (0.61) 비율이 1.5 및 0.5보다 높기 때문이다. 그럼에도 불구하고, 프린트 침전물 definition은 페이스트 점착성, 페이스트 유변학적 거동 그리고 니켈 표면과의 상호작용 조사와 같은 본질적인 페이스트 특성에 개입함으로써 더욱 향상 될 수 있다.
개구 벽면 및 니켈 스텐실 표면의 매끄러움이 향상됨에 따라, 페이스트 롤, 개구 충진 및 페이스트 방출 최적화를 개선할 것이다. 니켈 경도의 증가는 또한 웨이퍼와 스텐실 사이의 개스킷(gasket)을 현저하게 향상시킬 것이고, 결과적으로 침전물 간의 거리는 후속 페이스트 리플로우 공정에서 보다 안전해질 것이다.
Type 6 페이스트를 이용해 100㎛ 피치로 프린팅하는 것은 Type 8 페이스트로 프린팅하는 것과 비교하여 더 빈약한 definition의 프린트 침전물을 보였다. 그 이유는 Type 6 페이스트 파티클에 비해 50㎛ × 125㎛ 개구에서 Type 8 페이스트의 패킹 밀도(packing density)가 훨씬 더 우수하기 때문이다. 이후에 프린트 definition와 페이스트 점착력에 영향을 준다.
100㎛ 피치에서의 인쇄 aspect 및 area 비율이 1.5와 0.66보다 컸지만, Type 6의 페이스트 방출은 Type 8 페이스트보다 더 나빴다. Type 8 페이스트의 미세한 파티클 사이즈와 개구 내의 더 커다란 파티클 패킹 밀도(~10)는 페이스트 방출과 프린트 definition에 중요한 역할을 한다는 것을 의미한다.
범핑 결과 & 토론
60㎛ 피치 및 100㎛ 피치의 웨이퍼를 Type 8와 Type 6 페이스트로 각각 프린트한 다음, 산소 농도 20ppm 미만의 불활성 분위기에서 리플로우하였다. Type 8 페이스트의 리플로우에서 작은 솔더 볼이 많이 생성하였다. 게다가, 플럭스 블리딩(flux bleeding)은 리플로우 동안 메인 범프에 완전하게 합쳐지지 않을 수 있는 침전물(그림 6 참조) 사이에서 파티클을 옮길 수 있고, 범프에 얇은 볼로 나타날 수 있다. 솔더 볼링은 Type 6의 100㎛ 피치에서의 범핑보다 60㎛ 피치의 범핑에서 훨씬 더 일사불란했다. 다른 한편으로, 스크린프린터가 허용 가능한 최소한의 오프셋을 이용해 패드와 개구가 매우 훌륭한 정렬이 이룰 수 있도록 하는 것이 60㎛ 범핑에서 매우 중요하다.
그렇지 않으면, 인접한 침전물들이 합쳐져 브리징 또는 솔더 스틸링(solder stealing)을 초래하고, 이어서 불량한 범프의 동일 평면성을 생성하게 된다. 60㎛ 피치로 범핑하면 28㎛±3㎛ 높이의 범프가 생성된다. 100㎛ 피치의 범프는 42.3±3.8㎛의 높이를 가지고 있다. 그림 7은 60㎛ 피치의 범프가 있는 칩의 모습을 보여주고 있다.
그림 8은 60㎛ 피치의 범프 단면도를 나타내고 있다. 범프 높이 측정치는 광학 현미경 측정치와 잘 일치했다. 그림 9는 60㎛에서 범프 칩의 범프 높이 분포를 보여주고 있다. 10㎛의 전단 높이에서 50㎛/sec의 전단 속도로 가해진 범프의 전단 시험은 7.8kg/㎟의 전단 강도 값이 산출되었다. 전단 파괴 모드에서는 Sn63Pb37 솔더에서 균열이 발견되었다. 파괴 모드는 그림 10과 같다.
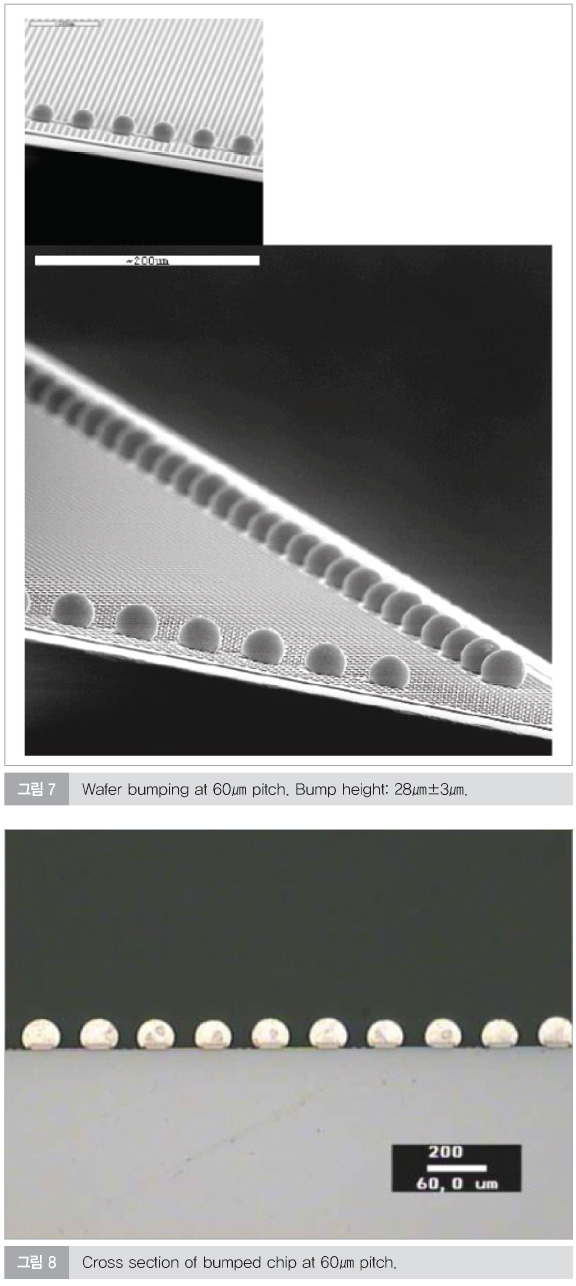
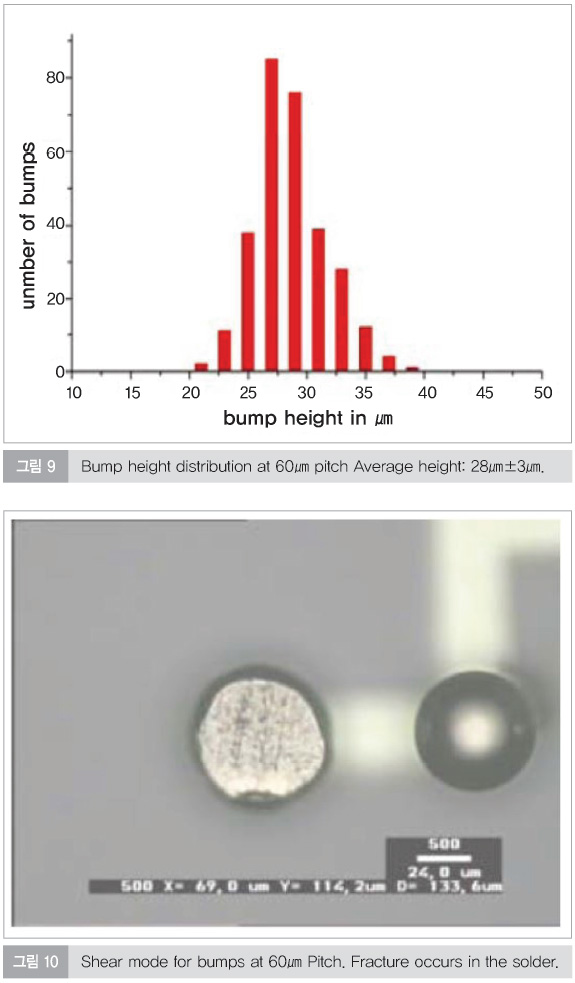
결론
Electroform 스텐실을 이용해 100㎛ 및 60㎛ 피치로 인쇄하면 초미세 피치의 범핑에 상당히 유리하다는 결과가 나왔다. 60㎛ 피치에서의 범프 높이는 28㎛±3㎛이었다. 새로운 Type 8 페이스트 (2~8㎛)를 개발하여 60㎛ 범핑에 사용하였다. 더 부드럽고 단단한 니켈 스텐실 제작은 UFP 웨이퍼 범핑을 위한 electroform 기술의 차세대 개발 단계가 될 것이라고 전망한다.