충분한 플럭스 양이 우수한 홀 충진 이뤄
솔더 브릿지, 전용 툴 적용을 추천
실험에서는 두껍고, 고열량의 보드 상에서 매우 미세한 피치의 부품을 우수한 홀 충진과 어떠한 브릿징 없이 납땜하는 것이 가능하다고 보여주었다. 홀 충진의 경우, 플럭스 양이 중요했다. 충분한 플럭스 활성제가 존재했을 때, 설비가 적절하게 설정되면, 심지어 10층의 Cu-레이어에서도 배럴은 100% 홀 충진을 보일 것이다. 브릿징을 피하기 위해서는 솔더의 융점 이상의 온도에서 적절한 질소 플로우와 가스를 분출하는 솔더 드레인 컨디셔너(SDC, solder drainage conditioner)와 같은 디-브릿징 툴이 필요하다. 솔더 볼은 솔더 영역에서 솔더 레지스트를 제거함으로써 제한될 수 있다. 각 플럭스는 서로 다른 특성을 보이며, 한 플럭스는 다른 것보다 더 많은 솔더 볼이 나왔다. 솔더 파라미터는 솔더 볼의 수에 영향을 주었다.
요약
PCB의 스루홀 부품의 수는 지난 10년 동안 크게 줄어들었다. 전자기기의 소형화로 인해 THT(through-hole technology)가 줄어들고 피치 간격이 더 좁아졌다. 이러한 이유로 이들 부품의 솔더링 방식도 웨이브 솔더링에서 포인트-투-포인트 셀렉티브 솔더링 방법으로 변경되었다. SMD가 PCB 레이아웃에서 THT 부품에 매우 가까이 위치할 때 이들 소형 미세 피치 부품을 솔더링하는 것은 어려운 문제이다. 본 고에서는 대형 자동차 EMS 고객과 협력하여 미세 피치 부품의 스루홀 기술에 대한 프로세스 윈도우를 규정한다. 솔더링 할 수 있는 것을 결정하고, 어셈블리 상에서 SMD 영역과 기타 부품을 가지고 솔더링이 가능한 레이아웃 디자인 파라미터를 규정한다.
서문
포인트-투-포인트 셀렉티브 솔더링은 세 가지 주요 목표가 있다; 우수한 홀 충진, no-브릿징 및 솔더 볼링 최소화. 보드 디자인에서 많은 파라미터가 솔더링 결과에 영향을 준다. 배럴의 홀 직경은 부품의 치수와 관련이 있다. 직경이 너무 작으면 핀을 부드럽게 삽입할 수 없고 손상될 수 있다. 직경이 너무 크면 갭이 너무 커서 솔더를 고정시킬 수 없으며 솔더가 빠질 수도 있다.
브릿징은 패드와 홀 직경, 리드 돌출 길이, 리드 직경/치수 그리고 리드의 피치에 영향을 받는다. 피치가 좁을수록 브릿지 없는 솔더링에 대한 도전과제가 높아진다. 일부 리드가 둥근형인 반면 다른 리드는 정사각형 모양이다. 브릿지 여부는 솔더의 모세관 현상(capillary action)에 달려있다. 이것은 중력과 같은 외부 힘의 도움으로 좁은 공간에서 흐르기 위한 솔더의 성능이다. 온도 및 유동성과 같은 솔더 특성은 모세관 현상에 영향을 미친다.
솔더 볼링은 또 다른 도전과제이다. 근본적인 원인과 관계없이, 솔더 웨이브를 떠날 때 솔더 볼이 솔더 마스크에 부착되지 않으면 문제는 대부분 없어진다. 최고의 솔더 마스크를 선택하는 것이 보드 설계를 강력하게 만드는 최상의 솔루션이다.[1]
테스트 보드
미세 피치 부품을 솔더링 할 때 주요 도전과제는 어떠한 솔더 브릿지도 나타나지 않게 하는 것이다. 일부 대량의 고열이 필요한 어셈블리의 경우, 홀 충진이 어려울 수도 있다. 서로 다른 설계 파라미터의 영향을 이해하기 위해, 솔더의 홀 충진 조사를 목적으로 서로 다른 레이어로 제작된 테스트 보드(2, 4, 6, 8 및 10레이어)를 사용했다. 이 테스트 보드에는 솔더 프로세스 윈도우를 확장하는데 필요할 수도 있는 모든 디자인 기능들을 포함하였다. 이러한 기능에는 솔더 마스크, solder thief, 5가지 피치(1.00, 1.27, 1.50, 1.75 및 2.00mm)에 있어서 서로 다른 홀 및 패드 직경이 포함되어 있다. 솔더성은 금속 표면의 상태에 영향을 받기 때문에 두 가지 다른 금속화제(immersion Sn, Cu OSP)를 서로 비교했다. 테스트 보드 치수는 285×184×1.6mm로 하였다. 어셈블리에 총 3,370개의 홀이 존재한다. 보드를 평평하게 유지하기 위해 팔레트를 사용하였다.
설비 및 구성
테스트는 셀렉티브 포인트-투-포인트 솔더링 머신에서 진행하였다. 설비는 고주파 드롭젯 플럭서(high frequency dropjet fluxer), IR(적외선) 히터 그리고 마그네틱 펌프-구동 솔더 포트로 구성되어 있다. 솔더 노즐은 조사된 파라미터 중 하나이다. 테스트에서 wettable nozzle과 non-wettable nozzle을 비교했다. 브릿징을 피하기 위해 SDC(solder drainage conditioner)를 솔더 노즐 뒤편에 설치하였다. 이 유닛은 커넥터 리드 사이에 뜨거운 공기를 불어준다. 가스 온도는 솔더의 융점보다 훨씬 높고, 플로우는 분당 7리터로 고정했다. 실험 동안 솔더 온도는 300℃였으며 합금은 Sn3.0Ag0.5Cu를 사용하였다. 예열 히터 전력은 51초 동안 45%로 가하여 상부 보드 온도를 120℃로 하였다.
실험 설계 - 홀 충진
첫 번째 실험에서는 홀 충진에 중점을 두었다. 솔더성에 영향을 끼치는 전통적으로 입증된 서로 다른 5가지 파라미터를 사용한 완전요인배치 설계(factorial design of experiment)를 선택했다. 이들 요인에는 플럭스 및 솔더링 파라미터가 포함된다. 플럭스 양과 타입은 두 가지 레벨에서 선택했다. 솔더 드래그 속도(접촉 시간), 노즐 유형 및 솔더 각도는 다른 요인이다. 솔더 온도가 홀 충진에 영향을 미치는 또 하나의 요인이기는 하지만, 300℃로 일정하게 유지하였다. 예열 설정도 일정하게 유지하였다.
테스트 보드에는 서로 다른 피치, 홀 및 패드 치수, Cu-레이어, 솔더 치프(solder thief)가 있으며, 솔더링 영역에서 솔더 레지스트를 제거했다. 이 실험의 목표는 보드와 프로세스 조건을 설계할 수 있도록 엔지니어에게 적당한 툴을 제공하여 고열량 보드에서 미세 피치 커넥터에 홀 충진을 충분하게 하는 것이다. IPC-A-610에 따라 양호한 홀 충전을 갖는 홀의 수를 카운팅하였다. 프린트 당 360개의 핀을 솔더링 시켰다.
보드 디자인은 차이점을 보여주기 위해 제작되었다. 10층의 Cu-레이어가 있는 프린트에 홀 충진 100%를 달성하기가 매우 어렵고, 모든 부품에 적합하지 않을 수도 있다. 이 테스트 보드의 목표는 한계를 찾는 것이다. 1.00mm, 1.27mm 및 2.00mm의 서로 다른 2열 핀 커넥터와 10개의 리드가 있는 1개의 1.50mm row 행 핀 커넥터를 솔더링하였다.
큰 영향을 미치는 두 가지 요소는 플럭스 양과 Cu-레이어의 수이다. 솔더가 구리 배럴로 흐르도록 지원할 수 있는 플럭스가 충분해야 한다. Cu-레이어의 열량이 너무 많은 열을 흡수하여 솔더가 보드의 상단에 닿기 전에 굳어졌다. 결론적으로, 열량이 높을수록 더 많은 플럭스 활성도가 필요하다. 플럭스 양과 Cu-레이어 간의 상호작용이 발견되었다. 그림 3에서는 충분한 플럭스 활성화로 모든 배럴의 홀 충진이 양호함을 보여준다. 심지어 10층의 Cu-레이어가 있는 홀에서도 양호했다.
Non-wettable nozzle은 솔더를 한 방향으로 흐르게 한다. 보드와의 접촉은 동일한 드래그 속도에서 더 길었고, 배럴에 가해지는 솔더의 힘에 더 많은 에너지가 존재했다. 따라서 non-wettable nozzle은 더 나은 홀 충전을 보여주었다.
주석침지도금(immersion Sn)은 홀 충진과 관련해 더 나은 보드 마감재이었다. 젖음성은 Cu OSP의 경우보다 약간 우수했다. 솔더링 전에 보드가 두 번 리플로우되기 때문에 Cu는 젖음 속도에 영향을 주는 작은 산화층을 가질 수 있다.
홀 직경도 중요하다. 보드는 서로 다른 피치의 서로 다른 직경을 지니고 있다. 1.27 및 1.50 mm 피치의 경우 0.80mm 직경이 가장 좋은 홀 충진성을 보였다. 2.00mm 피치의 경우, 바람직한 직경은 1.10mm이었다.
모든 부품은 사각형 리드를 지니고 있다. 치수는 1.27mm, 1.50mm 및 2.00mm 피치에 있어서 각각 0.35, 0.40 및 0.50이었다.
실험 설계 - 브릿징
우수한 홀-충진과 함께, 솔더 조인트의 브릿징을 피하는 게 중요하다. 부품의 돌출 길이가 더 짧으면 브릿징을 줄일 수 있지만, 이 결함을 제거하기 위해서는 브릿지 제거 툴(de-bridge tool)이 필요하다. 사용자는 돌출 길이에 영향을 받지 않으며, 모든 부품을 절단하는데 비용이 많이 들기 때문에 설비는 더 긴 리드를 처리해야 한다. 경험에 따르면 피치가 1.75mm 미만인 모든 부품에는 SDC 장치가 필요하다. SDC 장치는 액상 솔더에서 리드가 떨어지는 곳에 뜨거운 가스를 분출한다.
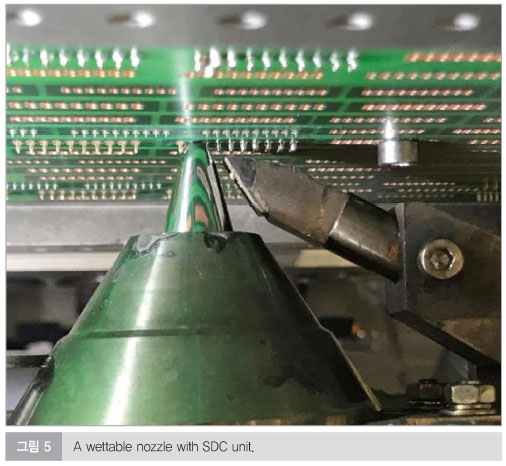
실험에서는 브릿징에 영향을 주는 몇 가지 부가적인 파라미터가 있었다. 솔더 치프(Solder thief)가 브릿지를 제거하기 위해 설계되었지만, 일부 무연 애플리케이션에서는 이점이 확인되지 않았다.
실험 설계 데이터를 사용하여 브릿징도 검사할 수 있다. 결과는 그림 6에 나와 있다. 점수가 높을수록 좋다는 의미이고, 360점은 브릿징이 없음을 나타낸다.
Non-wettable nozzle을 이용하여 브릿징이 적다는 데이터를 보여주고 있다. 3mm/s의 드래그 속도에서 더 좋은 결과가 나왔다. 홀 충진에 적합한 컨베이어의 기울기는 브릿징에 부정적인 영향을 미쳤다. 이는 평면 솔더링에 최적화된 SDC 각도를 변경함으로써 개선될 수 있다.
Cu-레이어에서의 영향은 주목할만하다. 확실하게도, 10층의 Cu-레이어 구조는 솔더 영역으로부터 많은 열을 흡수하여 브릿징 결과를 초래하는 솔더 응고가 더 빨라졌다.
솔더 치프(Solder thief)와 서로 다른 플럭스의 영향을 조사하기 위해 별도의 실험을 수행하였다. 패드 직경은 검토된 또 다른 요인이다. SDC는 브릿징을 제거하는 강력한 도구이므로 리드 돌출 길이는 중요하지 않다. SDC를 사용하지 않으면 브릿징을 피하기 위해 리드 돌출부가 짧아야만 한다.
패드 직경은 파인 피치에 있어서 중요했다. 1.27mm의 피치는 패드 외경 1.00mm에서 가장 낮은 결함을 보였다. 직경이 넓을수록 브릿징에 더 민감했다. 2.00mm 피치의 경우, 패드 외경 지름 1.50mm와 1.70mm 사이에서는 큰 차이가 없었다. 1.80mm 및 1.90 mm의 패드 외경 지름은 브릿징에 더 민감했다.
DOE(Design of Experiment)에서는 솔더 치프가 더 높은 솔더 속도에서 브릿징을 감소시킨다는 것을 보여주었다. 더 낮은 솔더 속도에서 솔더가 자체적으로 드레인될 수 있다.
솔더 치프는 솔더를 보드에 오랫동안 잡는다. Wettable nozzle은 보드에서 솔더를 박리하고, 브릿징을 피하도록 설계되었다. Wettable nozzle과 솔더 치프의 조합은 일부 무연 솔더 합금 애플리케이션에서 적합하지 않았다. 본 실험에서 이를 확인하였다.
솔더 치프는 패드에 솔더를 잡는다. 그림 8과 같이 솔더가 핀과 솔더 치프 사이에서 브릿징이 되지 않아 재작업을 피할 수 있다. 솔더 치프는 보드에서 더 많은 공간을 소비한다. 소형화로 솔더 치프를 추가하는 것이 중요할 수 있다. 10mm/s의 드래그 속도는 예외적이다. 실험에서는 올바른 파라미터 설정을 통해 어셈블리에서 반드시 솔더 치프가 필요하지 않다는 것을 증명하였다.
실험 설계 - 솔더 볼링
솔더링의 초점은 우수한 홀 충진과 브릿징에 중점을 두었지만 솔더 볼을 피하는 것도 중요하다. 솔더 볼링에 대한 이전 연구에서는 플럭스 유형과 솔더 마스크의 영향을 보여주었다. 테스트 보드에는 홀과 패드 직경이 동일한 3개의 스팟이 존재하지만 하나는 솔더 마스크가 있었고 다른 하나는 솔더 마스크가 없었다.
표 2에서는 솔더 마스크가 있고 없고의 차이를 보여주고 있다. 플럭스 A를 이 비교에 사용하였다. 실험에서 1.27mm 피치의 부품은 패드 사이에 솔더 마스크로 18개의 솔더 볼을 가지고 있으며 솔더 마스크를 제거할 때 솔더 볼이 없었다.
2.00mm 피치 부품의 경우, 유사한 차이를 보였다. 솔더 마스크를 제거할 때, 솔더 볼 수가 96% 감소했다. 회로 보드 상의 솔더 볼은 PCB의 솔더 표면의 플럭스 가스와 드레인의 결과이다.
솔더 볼이 보드 표면에서 발견된다는 사실은 플럭스 잔류물과 함께 솔더 레지스트에 솔더가 접착되어 있기 때문이다. 솔더 레지스트를 억제하는 것이 일반적으로 솔더 볼 접착 문제를 없앨 수 있지만, 항상 실행 가능한 옵션은 아니다. 솔더링 동안 솔더 레지스트의 약화가 솔더 볼 접착에 영향을 줄 수 있기 때문에 솔더 레지스터와 플럭스의 좋은 조합은 또한 이러한 접합 현상을 방지할 수 있다. 설비 설정을 최적화하여 이러한 접착 효과를 줄일 수도 있다. 그러나 일반적으로 이 문제는 올바른 재료를 선택해야만 해결할 수 있다. 솔더 프로세스 설정에서 솔루션을 찾는 것보다 예방이 항상 좋다.[2]
솔더 마스크 외에 플럭스가 솔더 볼에 영향을 미친다. 실험에서는 2개의 서로 다른 플럭스를 비교하였다.
R-sq = 56%는 솔더 볼에 대한 데이터가 일정하지 않음을 의미한다(80% 이상이어야 한다).
통계적으로 중요한 파라미터는 플럭스와 솔더 각도 간의 상호작용이다. 플럭스 A는 모든 조건에서 더 일관적인 모습을 보였다. 반면, 플럭스 B는 고속에서 수평적인 솔더링을 보이지 않았다. 일정 각도에서 솔더링할 때 SDC에서 나오는 질소는 납땜 직전에 보드 표면을 더 가열할 수 있다. 포트에서 솔더의 드레인이 부드러워지고, 줄어들면서 솔더 볼링이 된다. 솔더 마스크의 점착성은 SDC의 고온 가스에 의해 영향을 받을 수 있는 중요한 요소이다.
보드 휨
이전의 실험 동안 테스트 보드는 캐리어에 고정되어 평평하게 유지되었다. 보드를 납땜하기 전에 리플로우 오븐에 2번 통과시켰다. 일반적인 애플리케이션에서는 양면 리플로우 기술에 뒤이어 셀렉티브 솔더링을 한다. 리플로우 오븐의 뜨거운 환경에서 처리할 수 없는 스루홀 부품이 그 대상이다. 리플로우되었을 때, 보드는 뒤틀리고 더 이상 평평하지 않다. 재료 및 디자인(Cu-레이어 수 및 레이아웃)에서 얼마큼 휘어질지를 규정할 것이다.
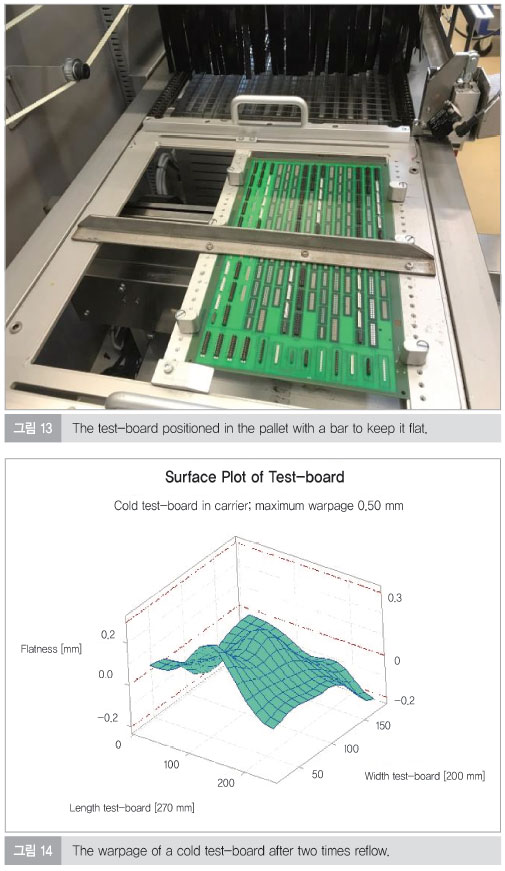
셀렉티브 솔더링 프로세스에서, 접촉 시간은 파동 높이, 솔더 포트가 장착된 로봇의 z-위치 그리고 보드의 바닥면까지의 거리의 함수이다. 셀렉티브 솔더링 프로세스 이전에, 기술된 바와 같은 히팅 사이클로 인해 보드가 휘어질 수 있다. 공정의 일관성을 위해 이 파라미터는 일정하게 유지되어야 한다. 보드 휨 보상 솔루션은 PCB까지의 거리를 일정하게 유지하는 옵션사항이다.
실험에서 예열 온도는 테스트 보드의 상면에서 100℃로 측정되었다.
테스트 보드 솔더링 전에 캐리어에 놓았고, 휨은 정밀한 레이저 센서를 이용하여 측정하였다.
예열로 인해 0.10mm의 최대 휨이 약간 늘어났다. 캐리어 없이 보드를 컨베이어에 놓았을 때, 휨이 훨씬 더 커졌다.
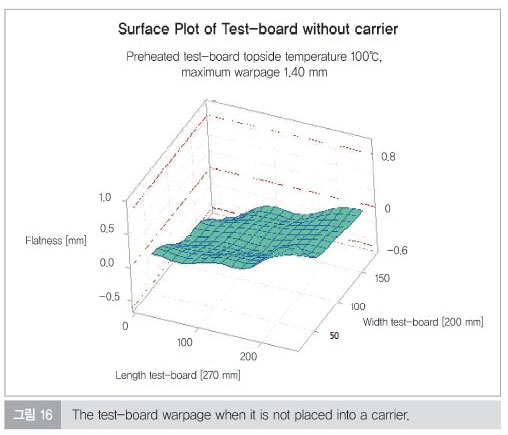
테스트 보드가 내부 10층의 Cu-레이어 구조로 매우 견고해 보이지만, 캐리어에 고정되어있을 때보다 훨씬 더 많이 휘어졌다.
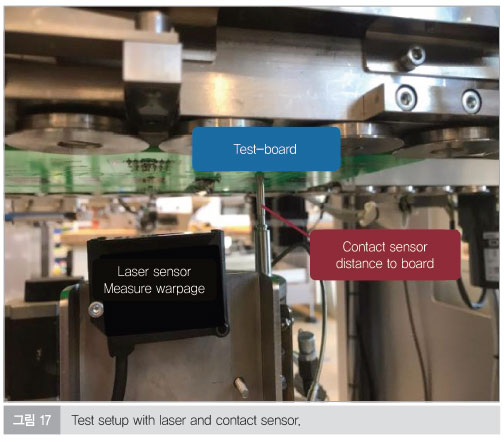
1.00mm 이상의 높이 차이는 오픈 솔더 조인트를 초래하거나 혹은 보드가 솔더 노즐에 부딪힘으로써 더 나쁜 결과를 유발할 수 있다. 이를 극복하기 위해서는 소프트웨어가 지능적이어야 하고, 보드의 휨에 따라 로봇의 z-축 높이를 수정해야 한다.
다음 실험에서 10개의 보드를 예열하고 그림 17과 같이 정확한 접촉 센서로 휨을 측정했다. 총 9개의 포인트가 보드 하부를 측정하였다.
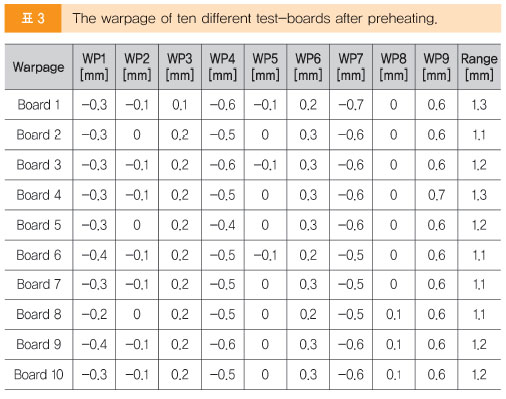
휨은 중요한 요인이다. 반복성이 뛰어나며, 대부분의 보드가 비슷한 모양의 휨을 갖는다는 점을 주의해야 한다. 접촉 시간에 대한 휨의 영향을 제거하기 위해 보드는 두 번째로 실행된다. 예열 이후, 휨이 측정되고 소프트웨어가 오프셋을 보정한다. 계산 거리는 접촉 센서로 확인된다.
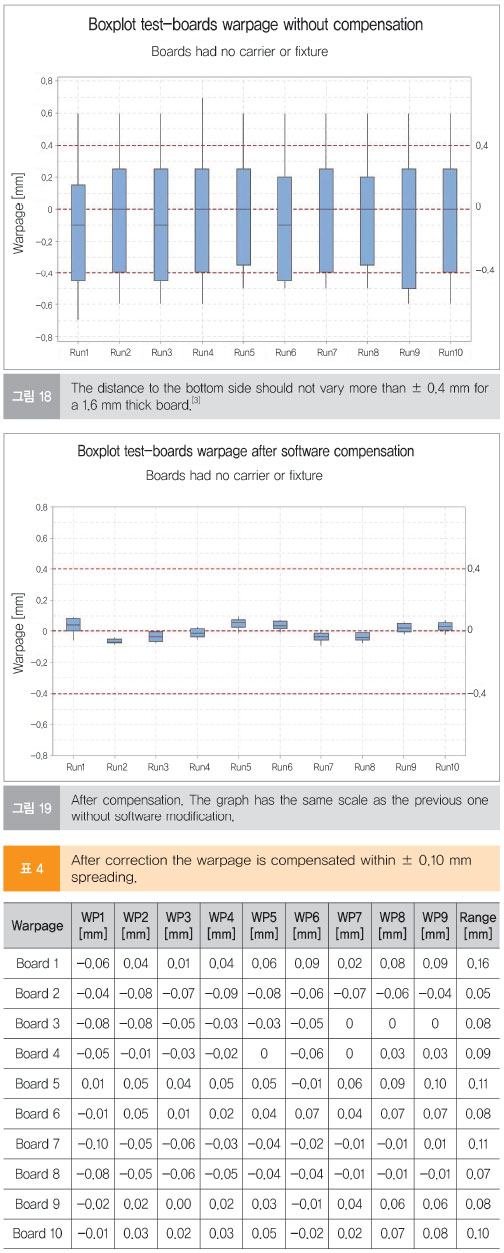
소프트웨어적인 보정은 노즐과 보드 하면 간의 차이를 최소화할 수 있다. 소프트웨어적인 보정 이후, 펴짐이 매우 협소해졌다. 모든 데이터 포인트가 ±0.10mm 내에 있었다.
실험에서는 보드가 자체적으로 평평해지지 않는다면, 휨 보정 없이 PCB를 솔더링하기가 어렵다는 점을 보여주었다. 프린팅 설계와 사용된 재료가 중요한 역할을 하였다. 또한, 셀렉티브 솔더링의 예열 프로세스와 같은 리플로우도 평탄도에 영향을 미쳤다.
결론
실험에서는 두껍고, 고열량의 보드 상에서 매우 미세한 피치의 부품을 우수한 홀 충진과 어떠한 브릿징 없이 납땜하는 것이 가능하다고 보여주었다. 홀 충진의 경우, 플럭스 양이 중요했다. 충분한 플럭스 활성제가 존재했을 때, 설비가 적절하게 설정되면, 심지어 10층의 Cu-레이어에서도 배럴은 100% 홀 충진을 보일 것이다.
브릿징을 피하기 위해서는 솔더의 융점 이상의 온도에서 적절한 질소 플로우와 가스를 분출하는 솔더 드레인 컨디셔너(SDC, solder drainage conditioner)와 같은 디-브릿징 툴이 필요하다.
솔더 볼은 솔더 영역에서 솔더 레지스트를 제거함으로써 제한될 수 있다. 각 플럭스는 서로 다른 특성을 보이며, 한 플럭스는 다른 것보다 더 많은 솔더 볼이 나왔다. 솔더 파라미터는 솔더 볼의 수에 영향을 주었다.
견고한 셀렉트-웨이브 솔더링 프로세스의 경우, 접촉 시간이 일정해야만 한다. 소프트웨어적으로는 레이저 센서로 휨을 측정하고 솔더 로봇의 z축-높이를 수정함으로써 보드의 하부면과의 거리 차이를 최소화할 수 있었다. 안정적인 웨이브 높이로 이 일정한 거리를 유지하면 우수한 홀 충진을 보장하고 어떠한 오픈 조인트가 나오지 않았다.
또 다른 대안은 보드를 평평하게 유지하기 위해 다운 홀더가 있는 팔레트를 사용하는 것이다.
REFERENCES
[1] https://www.epectec.com/pcb/wave-soldering-defects/solder-balls.html
[2] The origin of solder ball formation in wave soldering, Gert Schouten, Vitronics Soltec BV, 2006
[3] Position accuracy machines for selective soldering fine pitch components. APEX 2014, Gerjan Diepstraten, Vitronics Soltec BV.