고도의 자동화와 효과적인 테스트 방법은 오늘날의 산업계에서 점점 더 중요한 주제가 되고 있다. 현대 제조 기술의 진화는 공장을 보다 지능적이고 안전하며 또한 환경친화적으로 만들어 가고 있다. 실시간 정보를 제공하는 스마트 기기를 찾아내고 구현하는 것이 성공에 핵심이 되었다. 최근 생산라인에서는 2D/3D AOI가 성공적으로 활용되고 있다. 그러나 03015 부품에는 적합하지 않을 수도 있다. 따라서 본고에서는 AOI 공급 업체와 협력을 통해 초소형 부품 유형을 성공적으로 테스트하고, 최적화된 알고리즘 임계 값 설정을 통한 최상의 결함 탐지 성능을 이끌어 내는데 중점을 뒀다.
AOI(Automated Optical Inspection)는 제조 프로세스 초기에 결함을 감지할 수 있다는 점이 이점이다. AOI 시스템이 특정 부품(문제해결을 위한 추가적인 테스트 요구 억제에 실패한)을 식별함으로써 수리비용을 절감한다. 이 때문에 많은 EMS 회사가 특히, 새로운 타입의 부품에 대해 수리비용을 최소화하고 우수한 생산 프로세스를 유지하며, 고품질 생산을 위해 SMT 생산라인에 AOI를 적용하고 있다. 본 프로젝트는 AOI에 도전하는 03015 부품 패키지에 중점을 두고 있다.
고도의 자동화와 효과적인 테스트 방법은 오늘날의 산업계에서 점점 더 중요한 주제가 되고 있다. 현대 제조 기술의 진화는 공장을 보다 지능적이고 안전하며 또한 환경친화적으로 만들어 가고 있다. 실시간 정보를 제공하는 스마트 기기를 찾아내고 구현하는 것이 성공에 핵심이 되었다. 최근 생산라인에서는 2D/3D AOI가 성공적으로 활용되고 있다. 그러나 03015 부품에는 적합하지 않을 수도 있다. 따라서 본고에서는 AOI 공급 업체와 협력을 통해 초소형 부품 유형을 성공적으로 테스트하고, 최적화된 알고리즘 임계 값 설정을 통한 최상의 결함 탐지 성능을 이끌어 내는데 중점을 뒀다.
5대의 테스트용 보드(PCBA)을 이용해 5개의 AOI 벤더와 함께 테스트 작업을 진행했다. 각 PCBA 보드에는 3가지 피치 크기(100㎛, 150㎛, 200㎛)의 246개의 부품이 존재해 있다. 속성 Gage R&R, 불량 유출 및 호출오류 PPM(백만 분의 1)의 결과를 제시하였다.
매 세트의 데이터는 일부 3D AOI 기능을 갖춘 설비가 있었음에도 불구하고 2D AOI의 알고리즘을 적용하여 받았다. 이들 검사기들은 서로 다른 수준의 성능을 보여주었다. 5개의 AOI 시스템들의 데이터 분석 결과, 속성 Gage R&R의 측면에서는 아주 훌륭한 수용 가능 수준을 보여주었다. AOI 시스템 5와 AOI 시스템 6은 몇 퍼센트의 불량 유출 비율만 보였다. 그러나 본 연구는 초기 단계에 불과하다. 더 많은 개선 및 테스트가 수행되어야 할 것이다. 모든 공급 업체에게 새로운 테스트 결과를 지속적으로 제공할 것이다.
서문
PCB 어셈블리 산업계는 전자기기에 대한 ‘더 작고, 더 가볍고, 더 빠른’이라는 만트라(주문)을 오랫동안 받아 오고 있다. 특히, 최근 몇 년 사이에는 이러한 요구가 더욱 높아졌다. 어셈블리 업체들은 소형 부품에서 그 해답을 찾기 시작했다. 소형 부품의 사용이 증가함에 따라, 더 많은 고려사항들이 SMT 프로세스뿐만 아니라 테스트 공정에서도 이러한 변화를 연구하고 구현하기 위해 필요해졌다. 03015 부품에 대한 SPI(Solder Paste Inspection) 관련 연구가 일부 있지만, AOI에서의 권장된 관례는 극소수이다. 본고에서는 AOI 벤더와 함께 해당 프로젝트를 진행하였다.
03015(0.3㎜ × 0.15㎜) 디바이스는 마이크로 칩 부품이다. 참고로, 인간 머리카락이 대략 0.1㎜이다. 03015 부품의 성공적인 구현을 보장하기 위해서는 (1) 실장 설비 (2) 어셈블리 재료 (3) 공정 제어가 핵심 영역이며, 이 외에도 초소형 부품 타입을 테스트하는데 사용되는 시스템의 성능도 중요한 고려 사항 중 하나이다. 이제 3D SPI는 SMT 프로세스에서 일반적으로 사용되고 있으며, 3D AOI는 빠르게 늘어나고 있다.
연구의 초기 단계 동안, Milpitas 제조 현장에서는 2D AOI 설비를 이용해 03015 부품이 장착된 5개의 보드를 먼저 테스트했다. 다음으로 3D AOI 머신을 보유한 5개 AOI 벤더의 R&D 연구소에 보드를 보냈다. 다양한 R&D 엔지니어와 협력을 통해, 현재의 AOI 시스템의 도전과제(특히 부품 빛 반사로 인한 3D AOI 시스템의 한계)를 명확하게 확인하였다.
테스트 데이터와 결과에 따르면 다양한 2D AOI 설비들은 03015의 결함 유형(오정렬, 튬스톤 및 쇼트)을 감지할 수 있는 능력을 보유하고 있다. 호출오류 PPM이 증가하면 결함 유출 %가 줄어들었다. 따라서 최적화된 프로그래밍이 테스트 데이터 분석에 기반이 되어야만 한다.
실험 조건
총 5개의 AOI 벤더(R&D 엔지니어)에게 이 프로젝트와 함께 작업하도록 요청했으며 4 세트의 테스트 데이터를 받았다. AOI 시스템 3 데이터는 늦게 받아 이번 보고서에서는 제외시켰다. 테스트는 5개의 보드를 모든 AOI 머신에 동일한 조건으로 적용하였다.
테스트 보드
03015 부품이 장착된 5개의 보드를 AOI 시스템에 투입하여 테스트하였다. 그림 1에서는 서로 다른 피치 사이즈의 A, B 및 C 3개의 영역이 존재한 테스트 보드를 보여주고 있다. 피치 영역은 서로 다른 색깔의 화살표로 표시하였다(빨간색 A - 100㎛, 노란색 B - 150㎛, 파란색 C - 200㎛).
03015 부품은 완성품 레지스터로, 길이, 너비와 높이는 그림 2에서 보는 바와 같이 각각 292㎛, 143㎛, 및 100㎛의 제품이다(영역 A는 팹 마스크가 없음). A, B 및 C 영역에서의 총 부품 수는 각각 87개, 81개 그리고 78개였다. PCB 팹 상에서 패드 사이즈(길이, 너비)는 150㎛ × 150㎛이다. 그림 3은 영역 A(오른쪽 열), 영역 B(중앙 열), 영역 C(왼쪽 열) 그리고 프린트 이후(맨 위 줄), 실장 이후(가운데 줄), 리플로우 이후(맨 아래 줄)에 대한 그림을 보여주고 있다. AOI 테스트의 어려움을 증가시킨 03015 부품의 빛 반사로 인해 광학 그림에서는 다른 색상이 나타났다.
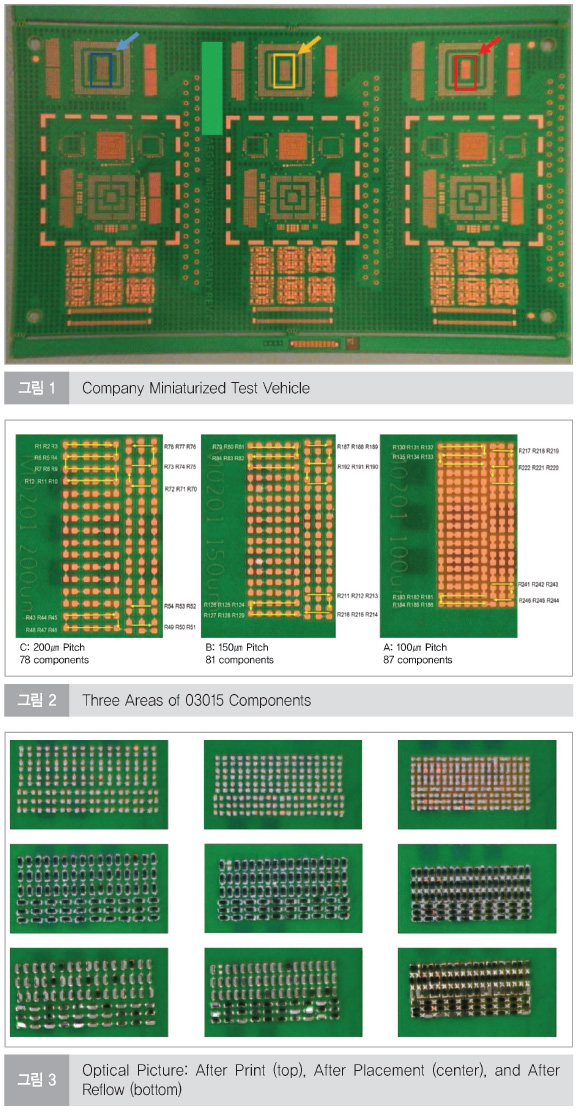
속성 GR&R
속성 GR&R 연구를 위해 피치 200㎛의 78개 부품이 실장된 보드 #4를 사용하였다. 총 9회에 걸쳐 보드를 테스트하였는데, 3명의 작업자가 각 3번씩 실시하였다. 그런 다음 속성 GR&R 데이터를 얻기 위해 생산 통계 소프트웨어를 사용했다. AOI 1, AOI 2, AOI 4, AOI 5 및 AOI 6의 속성 GR&R 데이터 결과는 그림 4와 같다.
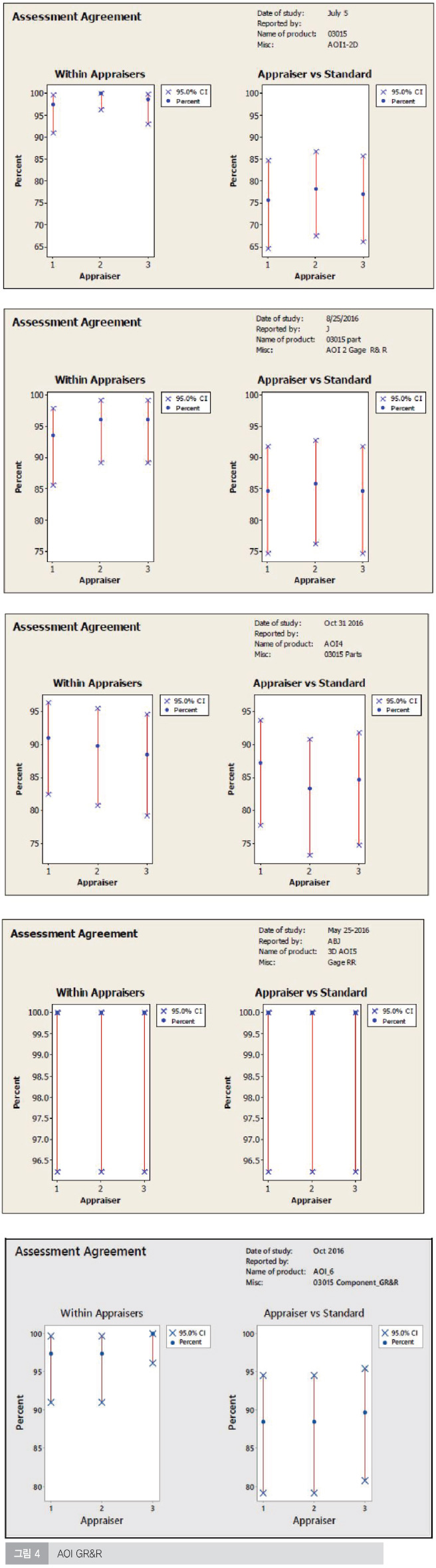
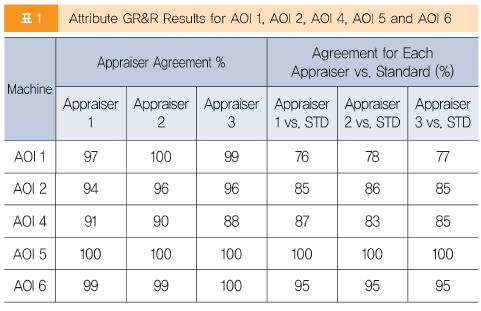
표 1에서는 AOI 시스템 1, AOI 시스템 2, AOI 시스템 4, AOI 시스템 5 및 AOI 시스템 6의 속성 GR&R 결과에 대한 ‘Appraisers agreement 비율’과 ‘Agreement for each Appraiser vs Standard 비율’을 보여주고 있다. 표준 결과는 AOI 설비와 현미경을 통해 얻은 사진들에 기반을 두었다. 그 결과는 또한 AOI 엔지니어의 discussion/agreement에 근거를 두었다. 이 5대의 AOI 설비는 Appraisers agreement 비율에서 매우 우수하거나 훌륭한 속성 GR&R를 가지고 있음을 명백하게 확인할 수 있었다. 각 ‘Agreement for Each Appraiser versus Standard 비율’의 경우, AOI 시스템 1의 결과는 괜찮았고, AOI 시스템 2 및 AOI 시스템 4 모두 양호한 결과를 보였다. AOI 시스템 6은 매우 좋은 결과를 나타냈으며, AOI 시스템 5는 최고의 결과를 보여주었다.
AOI 테스트 결과
이번 프로젝트에서는 서로 다른 AOI 설비로 5개 보드에 총 1230개의 부품들을 테스트하였다. AOI 1은 2D AOI이고, 나머지는 3D AOI 성능을 보유한 설비였지만 본 연구의 해당 단계에서는 3D 기능을 사용하지 않았다. 주요 두 항목(결함유출 %과 호출오류 PPM)은 각 AOI 시스템의 테스트 성능을 평가하기 위해 사용되었다. 부품 위치 결함은 회사의 엔지니어들과 AOI 이미지, 광학 그림들 및 광학 계측 설비에 기반을 둔 AOI 서플라이어들에 의해 확인되었다. 그림 5는 광학 계측 설비에서 얻은 사진이다. R1, R6 및 R7 부품이 결함으로써 미스얼라인되었음을 알 수 있었고, 부품 R3, R9, R15, R72, R75 및 R78은 AOI 이미지, 광학 이미지 및 엔지니어 검토 시 결함으로써 확인되었다.
그림 6에는 패드 피치가 200㎛인 동일한 보드 상에 동일한 24개의 부품이 실장된 보드를 5개의 AOI 설비로 검사한 이미지들이 나열되어 있다. 24개의 부품 위치의 경우, 9개가 결함이었다. AOI 시스템 1과 AOI 시스템 4 양쪽은 빨간색 직사각형으로 표시된 부문에서 1회의 호출오류가 나타났으며, AOI 시스템 6은 3회의 호출오류를 보였다. 그러나 AOI 시스템 2 및 AOI 시스템 5의 경우에는 표준 목록과 100% 일치하였다. 노란색 사각형은 부품 위치 결함을 나타내고 있다. 부품의 경면자재 재질이 설비에서 노이즈를 생성하기 때문에 03015 부품의 높이를 측정할 수 없었다. 그래서 모든 AOI 기계(AOI 시스템 2, AOI 시스템 4, AOI 시스템 5 및 AOI 시스템 6은 모두 3D AOI 설비)는 5개의 보드를 테스트하기 위해 2D 알고리즘만을 적용하였다.
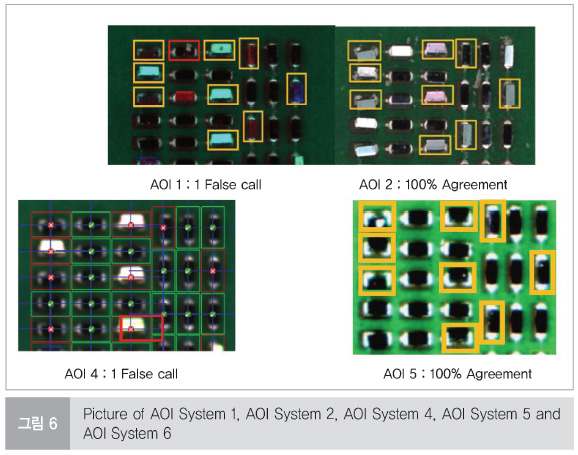
AOI 시스템 1, AOI 시스템 2, AOI 시스템 4, AOI 시스템 5 및 AOI 시스템 6의 AOI 알고리즘 임계 값은 표 2에 나열되어 있다. 이들 모든 알고리즘은 2D AOI 기능 알고리즘이었다. AOI 1 시스템은 카메라 레졸루션 향상을 위해 당사 사이트의 AOI 시스템 1 지원 엔지니어가 19㎛/pixel를 10.5㎛/pixel로 조정하였다. AOI 시스템 2는 6㎛ 레졸루션의 12Mpixel 카메라가 장착된 3D AOI 설비이다. 그러나 AOI 시스템 2는 03015를 테스트하기 위해 2D 알고리즘(PadMatch)을 사용하였다. 임계 설정은 Similarity : 55, Rotation : 4도, X-shift : 35㎛, Y-shift : 35㎛으로 하였다. AOI 시스템 4는 2D 알고리즘인 LW(Length and Width) 트랙킹을 사용하여 03015 부품을 테스트하였고, 이번 프로젝트에서는 임계 값을 XY ±35㎛으로 설정하였고, Theta의 경우, ±10㎛으로 하였다. AOI System 5의 주요 알고리즘은 다음과 같다: 분류 매칭(Classification Match) 180, Rotation 5도, X-shift 35㎛, Y-shift 35㎛. AOI System 6의 주요 알고리즘은 다음과 같다: Horizontal Threshold : 100㎛; Vertical Threshold : 50 μm; Skew Threshold : 40㎛.
AOI 테스트 결과를 표 3에 요약하였다. AOI 시스템 5 및 AOI 시스템 6 모두 매우 양호한 결함 감지 비율을 가지고 있었다. 모든 설비의 호출오류 PPM가 5000PPM 미만일 것이라고 예상했던 당초의 기대치 보다 높았다는 점에 주목하였다. AOI 시스템 1의 데이터는 5개 보드 중 4개에 대한 데이터이며, 제한적인 성능으로 인해 3개 보드의 경우에 100㎛ 패드 피치를 포함하지 않았다. AOI 시스템 2, AOI 시스템 4, AOI 시스템 5 및 AOI 시스템 6의 데이터는 03015 부품이 있는 5개의 모든 보드에서 얻었다. AOI 시스템 4는 곧 설치할 새로운 카메라로 상당한 개선을 가져올 수도 있었다. AOI 시스템 2, AOI 시스템 5 및 AOI 시스템 6에도 개선 단계가 진행 중이다. AOI 시스템 3은 약간의 진행한 후에 테스트 결과를 제공할 것이다.
결론
03015 부품을 테스트한 결과, 현재의 AOI 설비는 서로 다른 레벨을 가지고 있다. 하지만 이번 프로젝트에 참여시킨 모든 AOI 설비는 2D AOI 기능만을 활용하였고, 3D 알고리즘은 부품의 빛 반사 문제로 인해 적용하지 않았다. 속성 Gage R&R 결과에 따르면, 5개의 설비 모두가 수용 가능한 수준이었고, AOI System 5가 탁월한 결과를 나타냈다.
현재 가지고 있는 데이터를 기반으로 AOI System 5는 결함 감지 %에서 최고의 성능을 발휘했다. 그러나 호출오류 PPM에서는 5000 PPM 미만의 설비는 없었다. 해당 연구는 이제 시작단계에 있다. 특히 3D 알고리즘을 활용하여 AOI 머신을 테스트하려면 빛 반사가 없는 더 많은 보드가 필요하다. 많은 AOI 시스템 업체의 R&D 팀에서 장비를 더욱 개선하고 있어서 3D 알고리즘을 활용한 03015 부품 테스트를 멀지 않아 진행할 것으로 예상하고 있다.